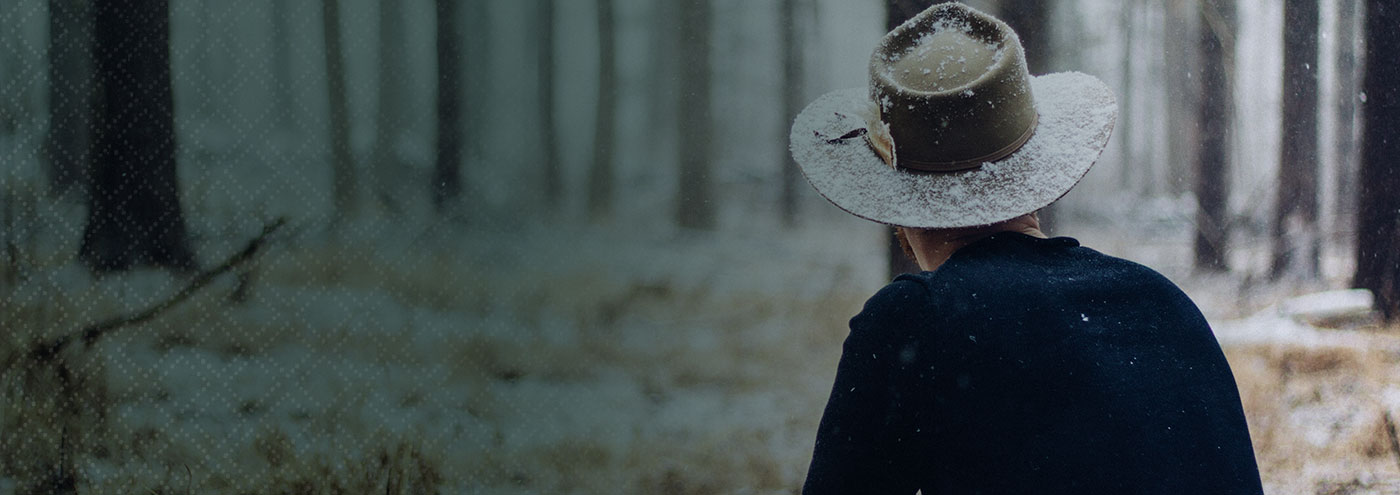
Experience. Wool.
TYPES OF WOOL AND PROCESSING
Shearing and grading
The first step in processing wool takes place on the farm or ranch with shearing, usually in the springtime. A skillful shearer, using electric hand clippers similar to enlarged barber’s shears, uses long, smooth strokes close to the skin in order to preserve the length of the fiber and hence the value of the fleece. Next come the buyers. Many times they take core samples of wool in order to measure fiber in length and diameter. Fine and medium-fine wools of longer staple lengths (more than three inches) usually go to make lightweight worsted suit and dress fabrics. Coarser and shorter fibers, less than three inches long, usually go into bulky sweater and carpet yarns.
Washing and scouring
The next step in the process is washing (scouring) the wool of impurities that can gather in the wool from the range, feedlot, or shearing floor.
Blending and dyeing
Clean wools from several different batches or lots are often blended—mixed mechanically—at this stage. Blending unifies the slightly different basic colors of raw wool, and also helps to standardize staple length and diameter for uniform quality. Each wool fiber absorbs dyes so deeply, that dyeing at any processing stage is equally effective and durable.
Washing and scouring
The next step in the process is washing (scouring) the wool of impurities that can gather in the wool from the range, feedlot, or shearing floor.
Blending and dyeing
Clean wools from several different batches or lots are often blended—mixed mechanically—at this stage. Blending unifies the slightly different basic colors of raw wool, and also helps to standardize staple length and diameter for uniform quality. Each wool fiber absorbs dyes so deeply, that dyeing at any processing stage is equally effective and durable.
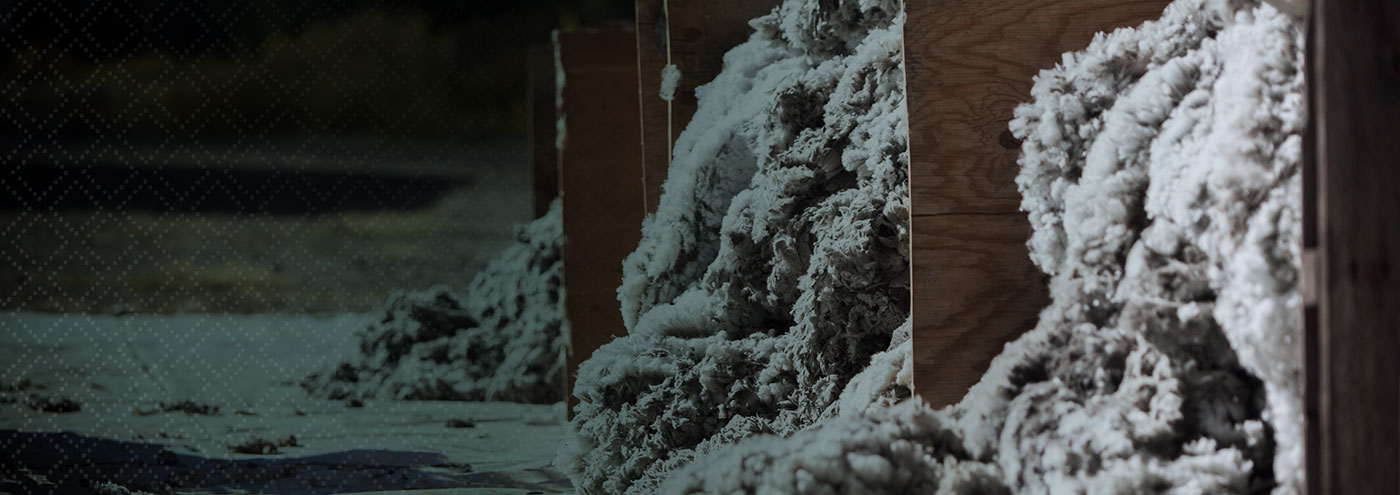
CARDING
The carding process passes the clean and dry wool through a system of wire rollers to straighten the fibers.
SPINNING
Next is the spinning process for yarn formation, which makes it ready for weaving or knitting. After spools of roving are in place on the spinning frame, the ends of the roving are drawn through small rollers to extend the wool fibers still further. Then the spinning machines twist and retwist the roving into yarns of a wide variety of qualities including strength, firmness, size, and ply.
WEAVING
Weaving produces cloth by interlacing two sets of yarn at right angles. Yarns running lengthwise in the loom are the “warp,” while yarns running crosswise form the filling or “weft.” As yarns are raised and lowered by cycles of the loom, a weft yarn is carried by a shuttle through the opening created by the warp yarns. This sequence, repeated endlessly, forms woven fabrics of almost infinite variety.
KNITTING
Knitting machines are just as versatile. Their mechanical needles are just as accurate and many times faster than hand knitting. Knitted fabrics are produced by interlocking rows of yarn and loops. As new loops are formed, they are drawn through those previously shaped. This interlooping and the continued formation of new loops produces knit fabric.
WOOLEN:
Woolen Fabrics are made of shorter wool fibers, giving them the added benefit of a fuzzy texture, such as a soft lambswool sweater.
WORSTED:
Worsted Fabrics are made from longer wool fibers that undergo an extra combing process. This creates a tighter spun yarn to be used in wool suits or your favorite t-shirt.
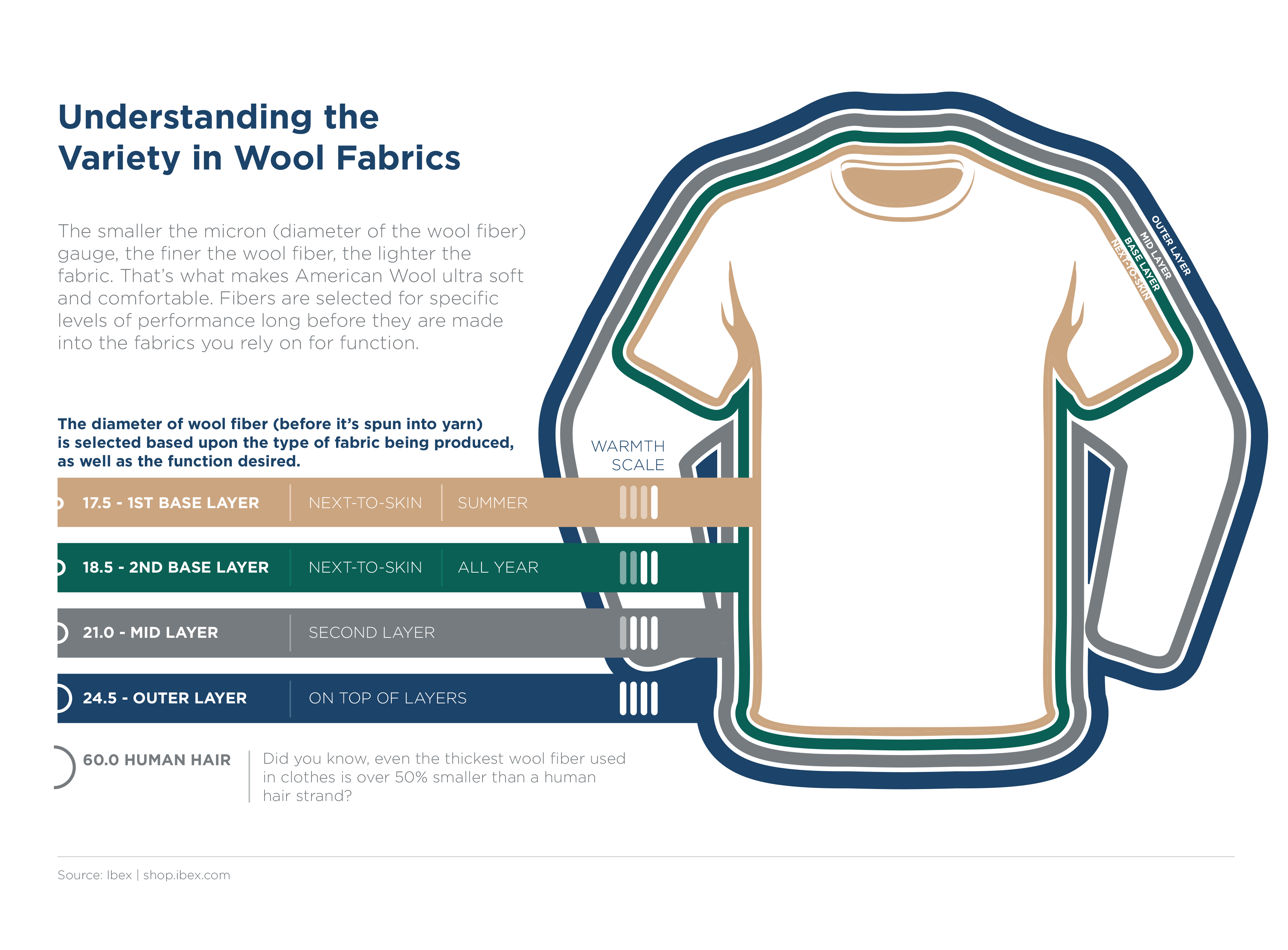
QUALITY CONTROL, FULLING, AND FINISHING
Quality control inspection is a part of the final step in fabric manufacturing. A thorough examination of the cloth identifies imperfections such as broken threads, variations in color, and other undesired effects. These are removed and the area is rewoven by hand if necessary
Once the fabric passes inspection, it undergoes a controlled shrinkage process called fulling or milling. Moisture, heat, and friction are applied, causing the fabric to shrink a controlled amount in both length and width. This tightens the weave and improves the hand (texture) of the fabric.
Woolens are often brushed to raise the ends of the wool fibers above the surface of the cloth in a soft, fluffy nap. Naps range from the lightly brushed surfaces of a flannel to the deep-pile effect of fleecy coatings.
FINISHES
Several finishes may be applied to wool, depending on their end use.
For washable wools, the finish reduces friction and fiber entanglement and eliminates felting shrinkage that usually occurs when wool garments are machine-washed and dried.
Wool can also be treated to make it highly resistant to moths, stains, moisture, and fire. The finishing process is the final step in wool processing, which takes the wool from the sheep’s back to woven or knitted fabric.